Visual Management in Lean Manufacturing
- Hakan Yasar
- Mar 16
- 3 min read
Updated: May 3

Visual management is a key part of lean manufacturing because it makes info and processes clear and easy to get. It uses things like signs, labels, charts, and color codes to show what's going on with operations and point out where you need to focus.
Discover the exciting ways visual management revolutionizes lean manufacturing!
Production status boards: These dynamic boards or screens keep you in the loop with real-time updates on production metrics, like the number of units produced, defect counts, and overall production status. With clear and concise displays, everyone can instantly see how things are moving along!
Andon systems: These vibrant visual signals alert workers to any hiccups on the production line. Imagine a flashing light signaling a machine halt or a quality issue—it's all about keeping everyone informed and ready to act!
Kanban boards: These powerful visual tools manage inventory levels and streamline production workflows. By moving cards or tags through columns as items progress, you can effortlessly track the status of each item and spot any bottlenecks in the process.
Standard work procedures: Visual aids like process flowcharts, work instructions, and standard operating procedures (SOPs) make it a breeze for workers to grasp their tasks. Displayed on the shop floor or at workstations, they offer a clear and concise reference for getting the job done right!
Using visual management tools in lean manufacturing can really boost communication, ramp up productivity, and cut down on mistakes and waste. It makes the work environment more efficient and effective, allowing workers to concentrate on activities that add value and make smarter decisions.
Kaizen Boards Gemba Meeting
Imagine the Possibilities with Effective Visuals!
When we don't harness the power of visuals effectively, several challenges can arise:
Clarity Boost: Visual aids are designed to simplify and clarify information, making it a breeze to understand! Without effective visuals, confusion can creep in, leading to misunderstandings and errors.
Efficiency Power-Up: Visuals are incredible tools for boosting efficiency in lean processes. If they're not clear or well-organized, they might slow things down, making tasks harder to complete swiftly and accurately.
Waste Reduction: In lean, minimizing waste is key! Ineffective visuals can lead to wasted time, resources, and materials, which is something we definitely want to avoid.
Consistency Champion: Effective visual aids are the backbone of standardizing processes in lean. Without them, variations can occur, leading to quality issues and inefficiencies.
Engagement Energizer: Visual aids can ignite worker engagement by clearly showing how their efforts contribute to the organization's goals. Ineffective visuals might lead to disengagement or frustration, impacting productivity and motivation.
Not using visuals effectively in lean can really mess things up. You might see things getting less efficient, more waste piling up, quality taking a hit, and workers not being as engaged. So, making good use of visuals is super important for a successful lean program.
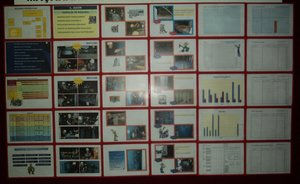
Here are some steps for effectively tracking progress from visual boards:
Tracking progress and identifying areas that need improvement from the visual boards are important tools in lean manufacturing.
Establish clear metrics: Before creating a visual board, it is important to define the metrics that will be used to track progress. This may include measures such as production volume, defect rates, or cycle time.
Set targets: Once the metrics are defined, set specific targets for each metric. These targets should be challenging but achievable and should be communicated clearly to all workers.
Update the board regularly: Visual boards should be updated regularly, ideally daily. This ensures that everyone has access to the most up-to-date information and can make informed decisions about how to improve performance.
Analyze trends: By tracking progress over time, it is possible to identify trends and patterns that can provide insight into areas that need improvement. For example, if defect rates are increasing over time, this may indicate a problem with a particular process or machine.
Take action: When issues are identified, take action to address them. This may involve implementing process improvements, providing additional training to workers, or making changes to equipment or materials.
Celebrate successes: When targets are achieved or progress is made, celebrate these successes with the team. This helps to reinforce the importance of tracking progress and motivates workers to continue to strive for improvement.
Comments